Water-based Zinc flake technology in serial production on passenger car chassis components
In today’s world, the automotive industry is increasingly striving to continuously improve its
environmental compatibility and ecological footprint.
This is already being successfully implemented in several areas of the process chain, whether
using new and more environmentally compatible materials or optimized processes.
An important factor here is to increase the service life of the components used in automotive
construction, and here, when metal parts are used, their effective protection against
environmental influences plays a significant role.
Particularly in the chassis area or underbody of the automobile, metal parts are exposed to
various weather conditions such as dirt, stone chipping, moisture, and salt loads in winter.
Optimum, long-lasting corrosion protection is therefore an important criterion for maintaining the
functionality of these components.
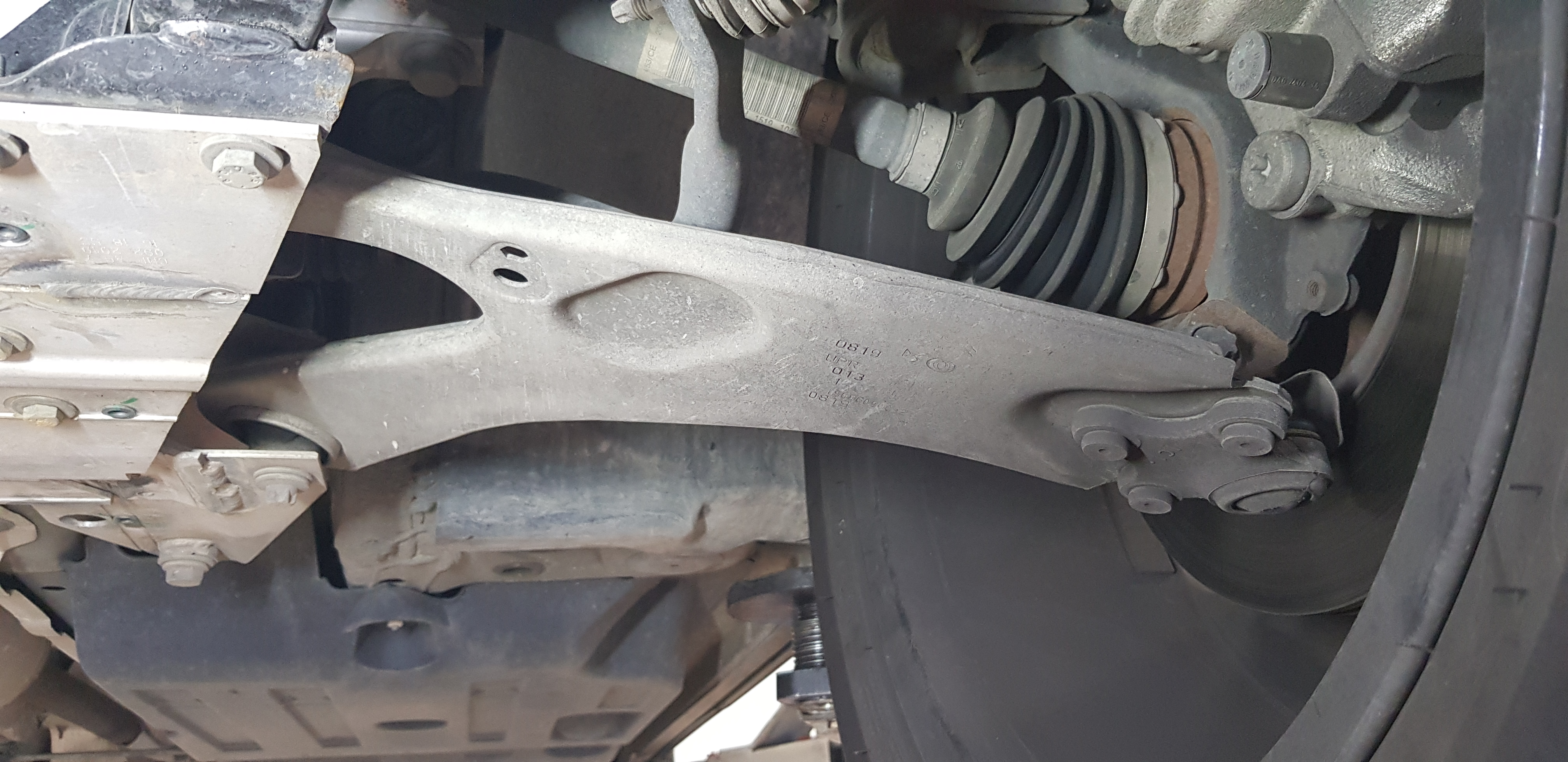
Chassis components – overview and requirements
Today’s standard coating for these components is the cathodic electrodeposition, usually in the
thick film range of 30-50 μm.
This coating process is very effective as a barrier layer against corrosion but shows weaknesses
if the surface of the coating is damaged (e.g., by stone chipping) and corrosive medium can thus
penetrate to the substrate surface. The metal corrosion that occurs in this area could lead in the
worst case to the complete failure of the component in question.
For this reason, the automotive industry is increasingly looking for alternatives to conventional
paint coating to effectively extend the service life of the components used.
There are various ways of increasing the protective effect of pure paint coatings. Electrocoat
layers, for example, could be combined with other coatings, which are referred to as «multi-layer
systems”.
However, the application of several different layers causes additional work with significant costs,
and these systems also quickly achieve total coating thicknesses in the range of over 100 μm.
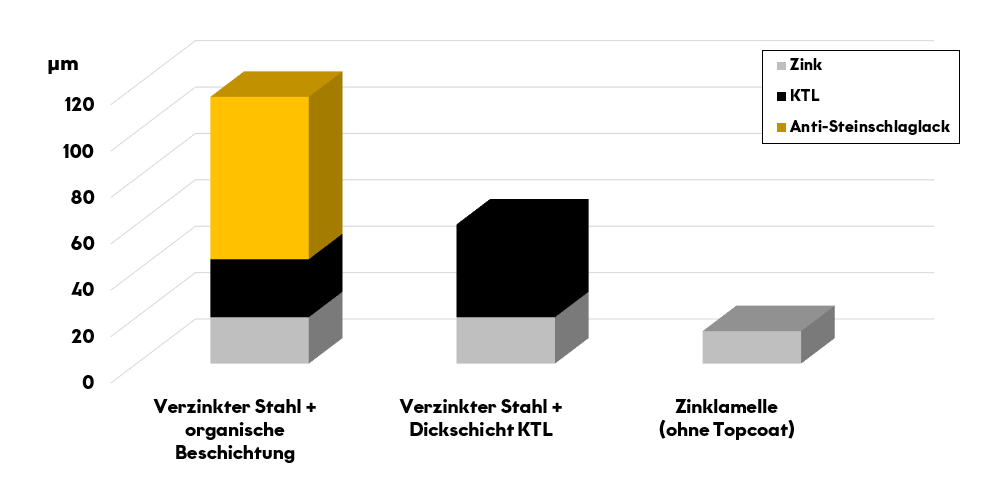
Another option is to cover the exposed components with plastic claddings so that they are not
directly exposed to the respective weathering influences, and here in particular to stone chipping.
With this method, however, in addition to the corresponding additional costs, the additional weight
of these claddings for the vehicle must also be considered critically.
Zinc flake – General properties
An interesting alternative to the protective measures described above is the use of socalled zinc flake technology on chassis parts, which offers increased corrosion protection with significantly thinner layers than comparable systems.
To apply zinc flake systems, the component is immersed in a medium consisting of a binder matrix with zinc and aluminum flakes. In this currentless process, a thin layer of a liquid film is first produced on the substrate surface. Then, by means of a spin-off process, a thin and uniform layer is formed on the component, which is crosslinked and firmly bonded to the substrate by subsequent baking.
Zinc flake technology has already been used successfully for decades, especially for coating bulk
small parts such as bolts, nuts and other fasteners, or on stamped and bent parts, and has the
following features, among others:
- Excellent cathodic corrosion protection.
- Thin layers (5-15 μm)
- Coating of hollow/recessed areas possible
- No chromium-containing or other heavy metals
- No hydrogen embrittlement (currentless application)
- Additional topcoats can be applied
The GEOMET® zinc flake coatings used by NOF Metal Coatings are exclusively water-based and thus have even more advantages from an environmental point of view compared to the other solvent-based systems available on the market.
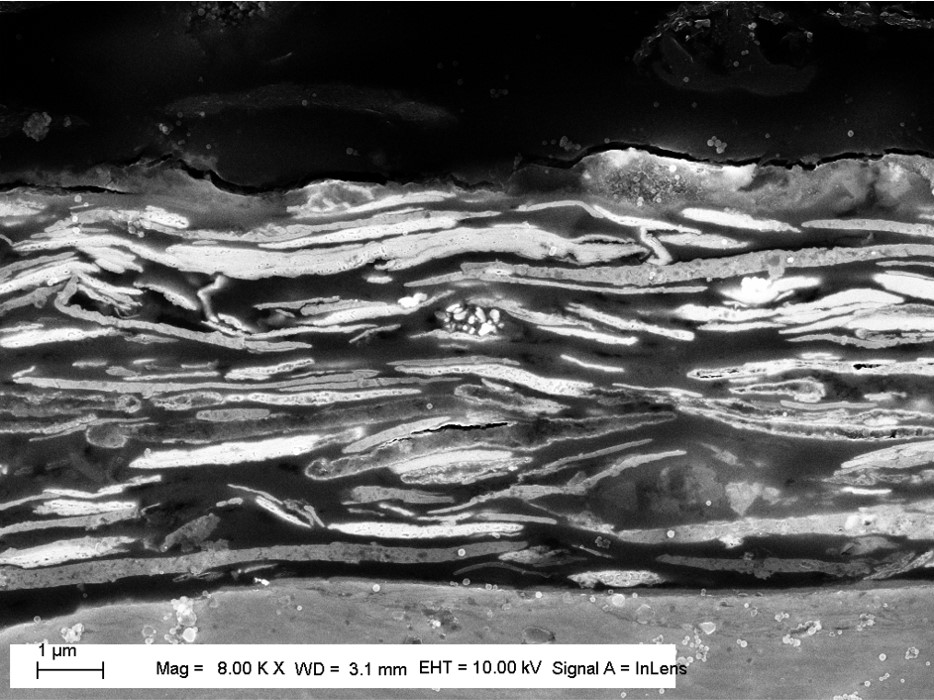
Low control arm with GEOMET®- zinc flake coating – qualification steps
Due to the advantages of zinc flake coating shown above, there is an interest on the part of
automotive manufacturers to use this technology also on chassis parts on a larger scale than
before. In the following, the individual steps from qualification to series production of the zinc flake
will be explained based on a specific application.
This involves the control arms of the front axle for the «Common Modular Platform» of the
company Stellantis.
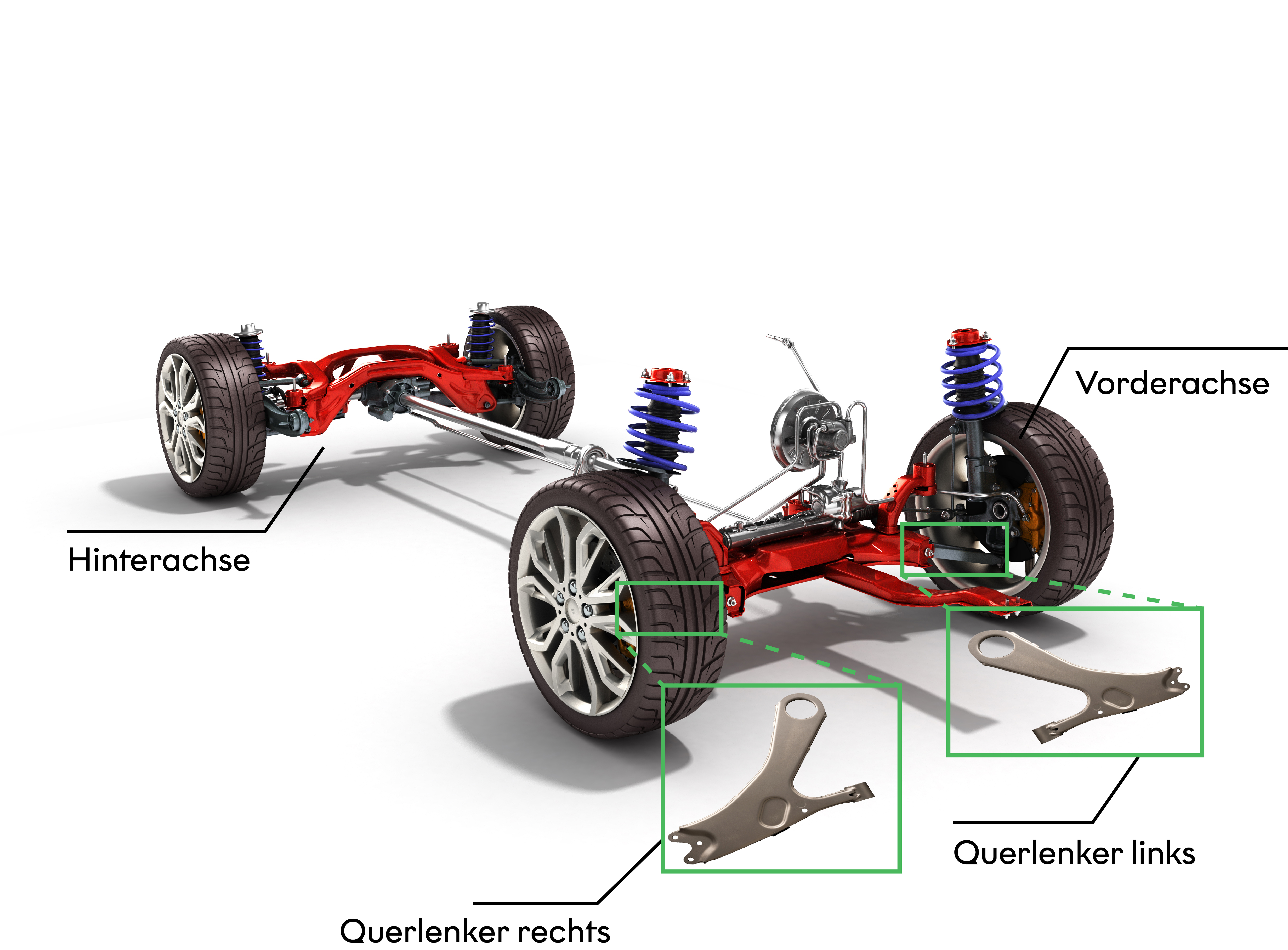
For this platform, the use of a double-shell low control arm has proven to be the optimum solution.
The use of pre-galvanized steel/coil for this component would be conceivable for reasons of corrosion protection, but the chosen part design requires welding of the two control arm shells. And this step carries the risk of porosity in the weld seam due to sublimation of the existing zinc, caused by the heat generated during the welding process. In extreme cases, this could lead to fracture of the weld seam and thus to complete failure of the control arm in series production.
To reduce this risk, the welding parameters would have to be adjusted when welding pre-galvanized steels and, above all, the welding speed would have to be significantly reduced, which would have a negative effect on productivity.
In this case, the zinc flake coating has provedto be an excellent alternative, because the control arm parts can be manufactured from ungalvanized steel, welded together and the coating is applied to the finished component only afterwards. This results in cathodic corrosion protection without the abovementioned risk for the complete control arm with unchanged welding parameters.
To qualify the GEOMET® zinc flake coating on the control arm, intensive test series were carried out
on coated components. The requirements or test criteria on the part of the OEM included various
mechanical tests and corrosion tests as well as a dynamic driving test.
The corrosion tests required were the neutral salt spray test in accordance with EN ISO 9227 (1000
hours) and outdoor weathering (12 months).
To better address the requirements in the underbody area, the test specimens were also treated
with a stone chipping test according to EN ISO 20567-1, method B, before the test series was
started.
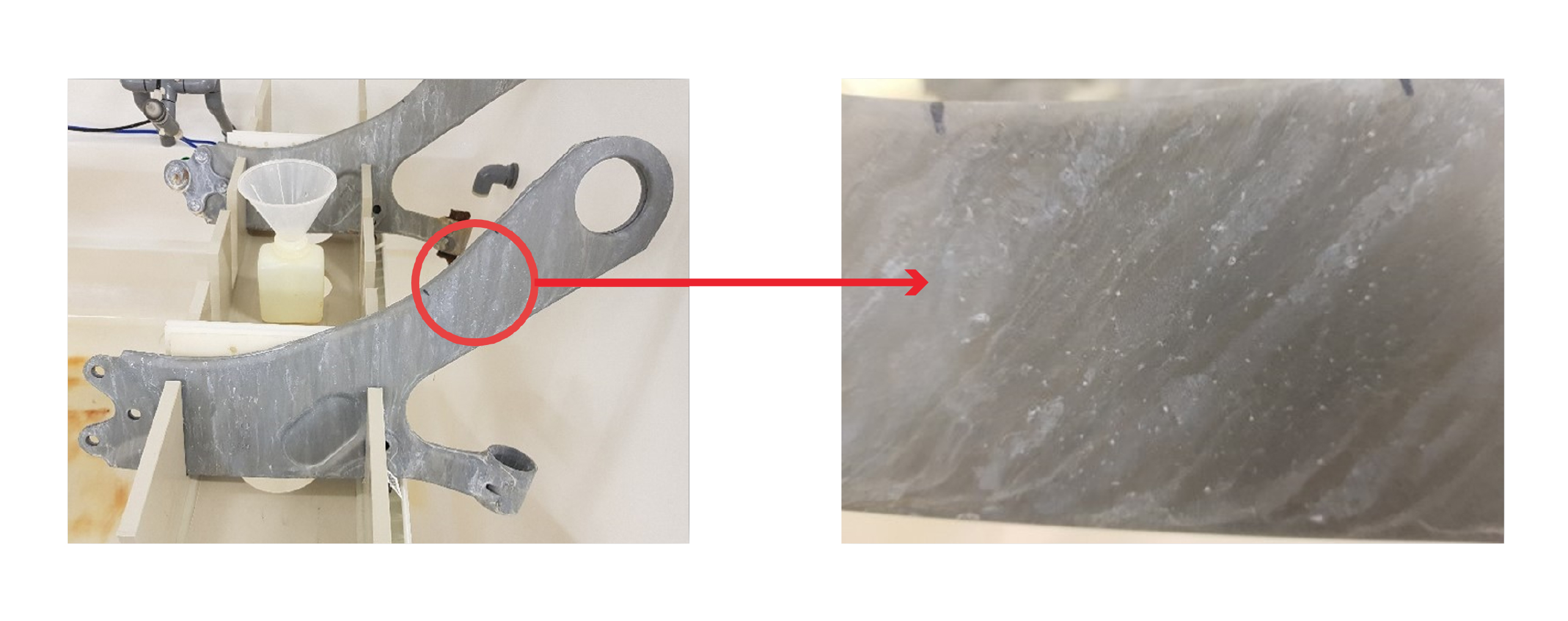
The outdoor weathering of the test specimens was carried out at various locations in France to represent both industrial atmospheres and maritime climates. In the dynamic driving test, the control arms coated with GEOMET® were installed by the OEM in test vehicles and then subjected to various loads on a test track, such as driving on a gravel track, cobblestones, and through a sand and salt water tunnel. In between, the vehicles were driven at regular intervals into a climatic room to expose it to high humidity and/or salt spray.
After various specified cycles, the control arms were checked for possible corrosion and functionality. The tests described here were carried out in close cooperation with the OEM and were examined and evaluated together. As a result of these tests, it can be stated that all test results exceeded the OEM’s quality requirements.
In the specific case of outdoor weathering as an important part of the «real-life scenario» of a vehicle, a component still shows no signs of corrosion for now over 60 months.
Based on these very positive results, the zinc flake technology was qualified and approved by the OEM as the only coating option for this control arm.
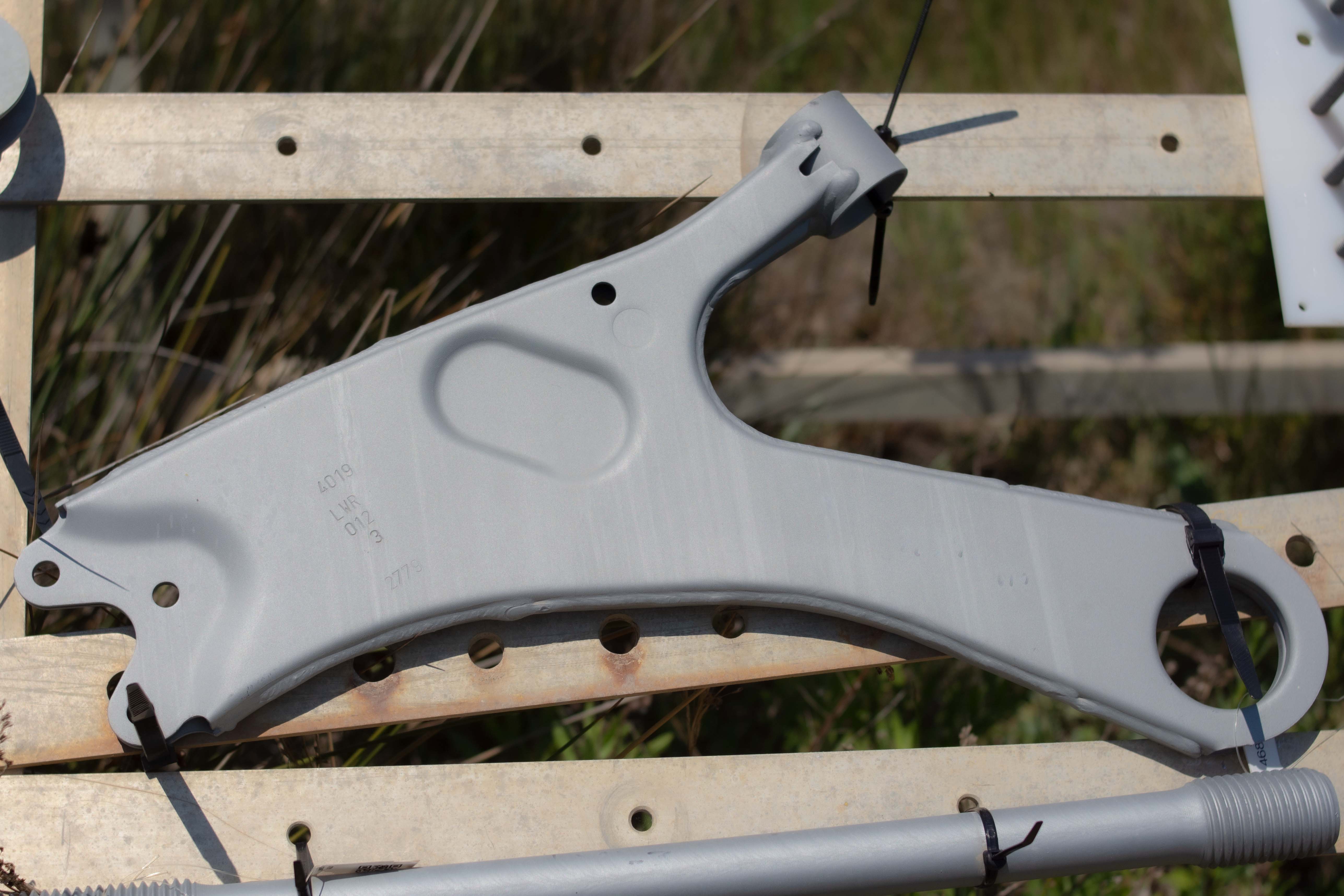
Control arm with GEOMET® zinc flake coating – serial production
The production site for the control arms is in Zaragoza, Spain, and the coating applicator «Aragonesa de Tratamientos» is in the immediate vicinity of TIER1, which has a positive effect not least in terms of logistics.
From Spain, the coated parts are shipped to the various OEM locations, where they are installed in the manufacturer’s corresponding models. This is a platform designed for compact SUV models, on which four different models are currently being fitted with these control arms.
In the serial production, the zinc lamination is applied through a dip-drain-spin process. Here, the rack design and positioning of the parts are decisive factors for maximum productivity with the lowest possible contact points of the parts. At the same time, correct dripping of the parts without local accumulation of liquid must be ensured.
The individual process steps are shown in detail below:
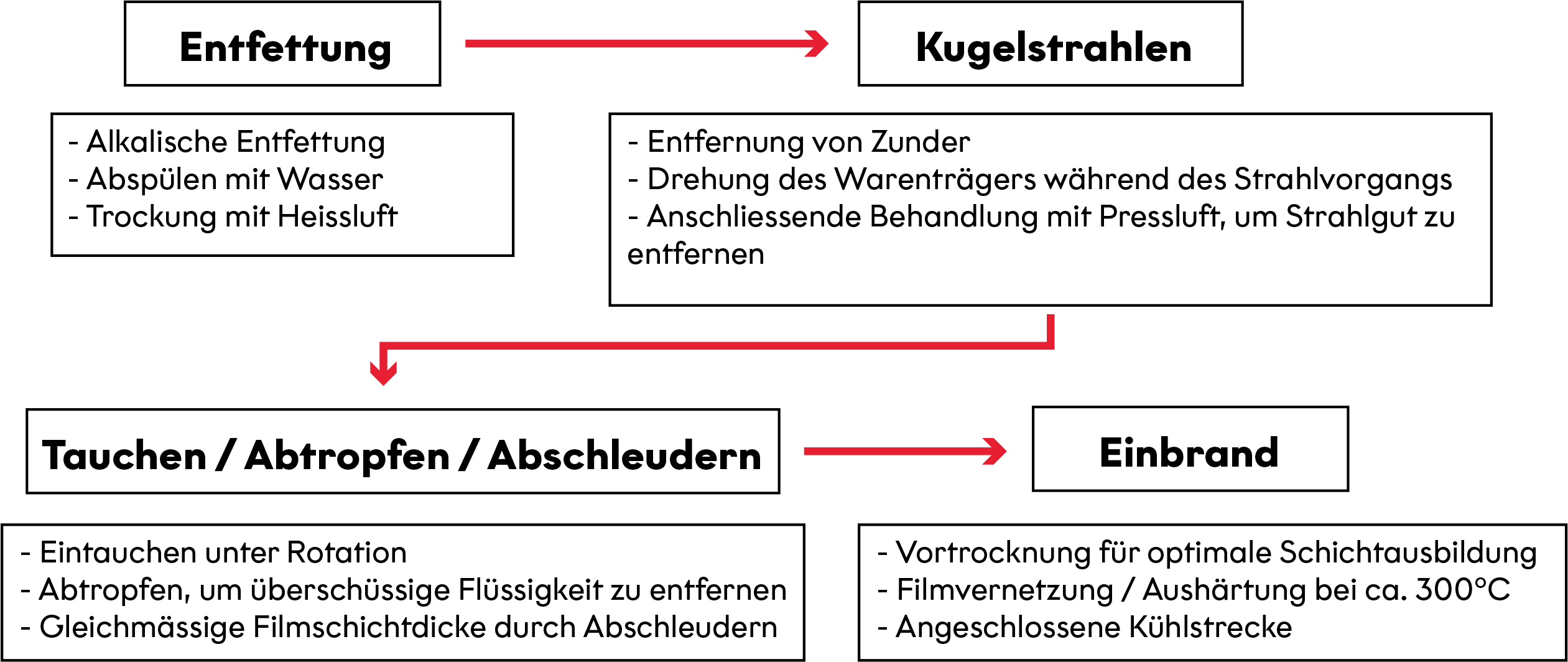
The dip/drain/spin and curing steps are repeated in this process, thus it is a 2-coat Zinc flake application. An additional topcoat or sealer is not required. With this described process, a uniform GEOMET® coating thickness of 11-14 μm is applied to the control arms.
Since the start of serial production in Spain at the beginning of January 2019, more than 1 million control arms have already been successfully coated to date, and accordingly more than 500,000 vehicles with these components are already on the road.
Summary and Outlook
Here is a short summary of the findings:
• The requirements for chassis parts are increasing with regards to longer service life of the individual components by reducing their weight at the same time
• The use of new materials such as high-strength steels and/or new construction methods (multi-layer structure) brings new challenges, especially for long-term corrosion protection
• Classical coating processes can only partially meet these new requirements
• Zinc flake technology as a coating alternative offers increased corrosion protection with lower coating thicknesses than comparable systems
• Initial field tests of control arms coated with zinc flake confirm the positive results from
the OEM approval tests
For the future, we see an expansion of the current platform to further models of the Stellantis Group and thus a further increase in the current control arm volume. In addition, several test series with other GEOMET® coated components have been successfully completed, so that we are in intensive discussions with further OEM’s/TIER 1’s for additional vehicle types.
In general, it remains to be said that there is great potential for the use of zinc flake technology in the chassis area and that new application opportunities are coming up, not least because of electromobility.