Parts
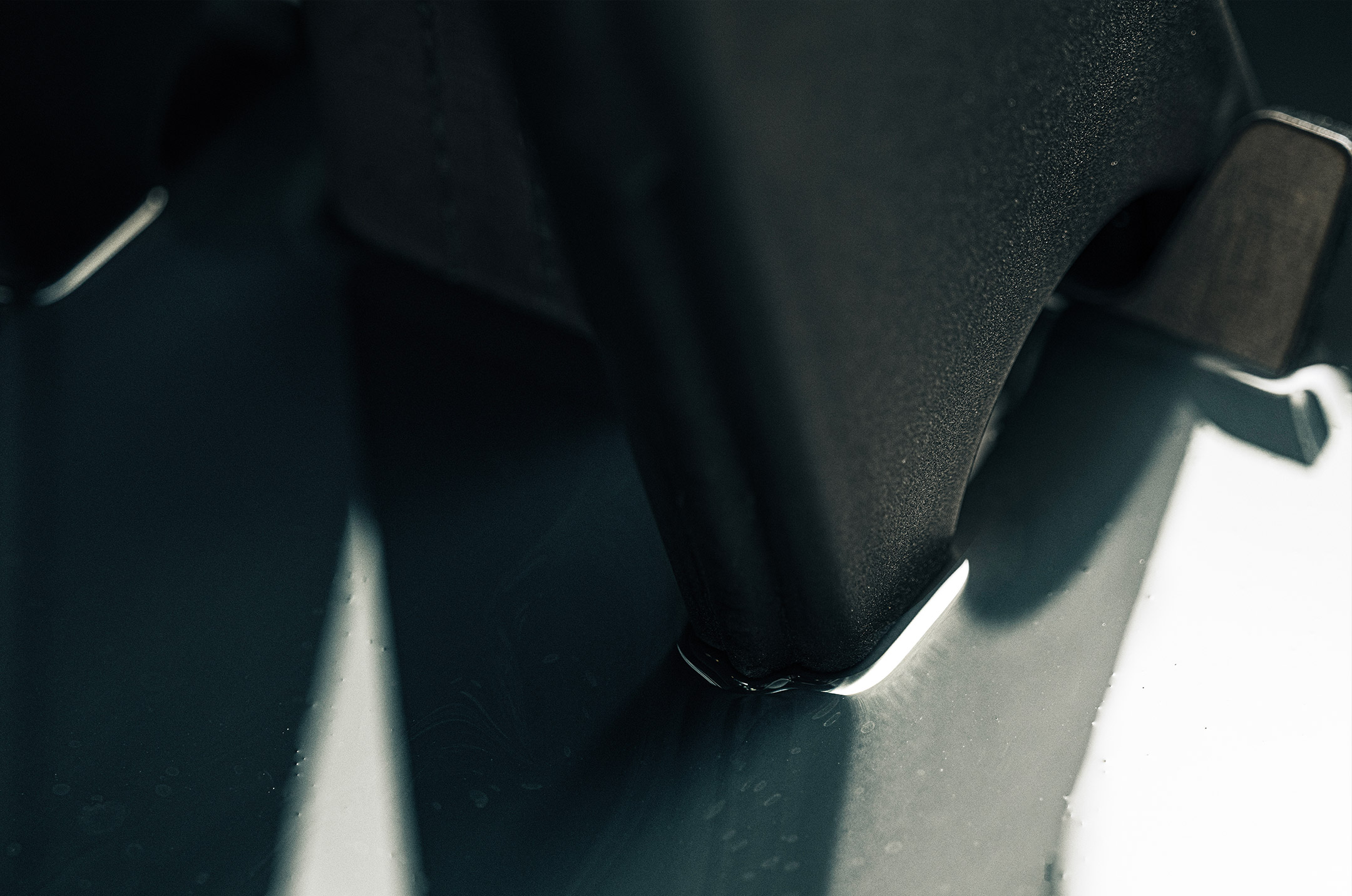
-
Sintered parts
This process allows to make complex shapes with powders. Many applications are done in rack coating. Part makers must clean porosities at the end of the process to avoid issues during coating.
-
Machined parts
This process allows to reach very precise characteristics and complex shapes. Coated in bulk or rack depending upon dimensions and geometry.
-
Casted parts
This process is used in many chassis and braking areas but with higher surface porosity than steel. A specific surface preparation depending on casting alloys is necessary before rack coating.
-
Stamped parts
This process is used for small-medium parts (brackets…) sometimes with additional process (welding, crimping…). As OEMs seek to reduce weight, the metal sheet lower thickness pushes to increase corrosion resistance. Parts are coated in bulk or rack depending upon dimensions and geometry.
-
Extruded pipes
Key requirement is to have a high external and internal corrosion protection on quite deep length which fits perfectly with non-electrolytical process like zinc flake. Parts are coated in rack dip-spin.
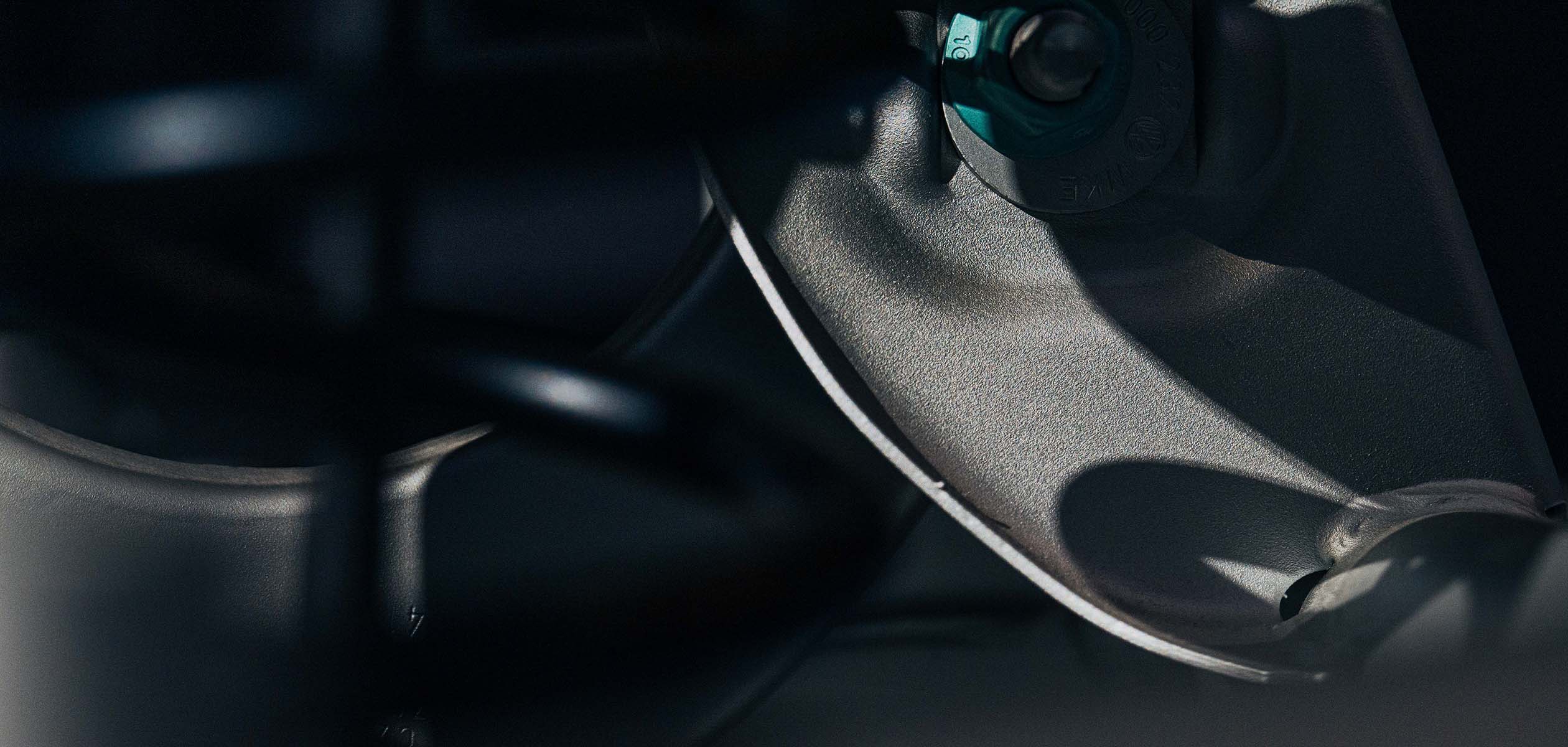
Find the coating that meets your requirements
From the choice of coatings and application processes to their industrialization, our teams put their know-how at your service to guide you towards the solution that fits your parts.
- Quality Policy
- Environment Policy
- Privacy Policy
- Website terms of use
- Cookies management panel
- © NOF Metal Coatings Group 2025