Environmental concerns in the DNA of NOF Metal Coatings Group
As the inventor of anti-corrosion zinc flake technology, NOF Metal Coatings Group has always been one step ahead of the competition in supporting the development of the fastener industry from both a technical and environmental point of view.
Since the late 1970s, with the launch of the famous DACROMET®, fastener manufacturers have had access to a high-performance, non-electrolytic anticorrosion technology capable of solving the problem of hydrogen embrittlement for steel grades 10.9 and above. This innovation has enabled fastener manufacturers to save the large amount of energy required to hydrogen de-embrittlement of electrolytic coating solutions. At the same time, it has helped accelerate the development of high-strength steel fasteners, reducing pressure on iron resources and steel production.
Improvements to our waterborne zinc flake coating technology, driven by new environmental regulations, led to the development of GEOMET®, which contains no form of chromium and still meets the fastener industry’s high demands for anti-corrosion performance. Since then, our technology has gone from strength to strength thanks to a wide range of customer specifications, particularly in the automotive, truck and renewable energy sectors.
Reduce industrial pressure on water and mineral resources
Our coatings are composed of zinc and aluminum pigments dispersed in a sol-gel matrix. Thanks to their unique formulation, GEOMET® coating systems are able to offer very high corrosion protection performance (over 2000h NSS) with a limited amount of metallic pigments compared to conventional anticorrosion coatings.
What’s more, its non-electrolytic coating process requires extremely low volumes of water and produces very little waste, bringing additional environmental benefits to our coating solutions, particularly at a time when natural resources have become even more precious than before.
Our zinc flake coatings are among the most efficient, competitive and environmentally friendly solutions available on the market. But climate change has become more than just a reality, and beyond our responsibility, NOF Metal Coatings Group staff are committed to contributing to the development of more sustainable and industrial coating solutions.
A global group committed to building a new future for our planet
By pooling the strengths and minds of our multicultural research and development teams, located in Europe, Asia and North America, our top priority is now to further reduce our environmental footprint, with existing and new solutions.
4 years ago, we started our first life cycle analysis with GABI, one of the most advanced software package available on the market. Our aim was to measure and understand the various impacts of our solutions on the environment, in order to prioritize our development activities appropriately.
This initiative has already given us a totally new perspective on our raw materials, chemistry and coating technology. We now have the opportunity to better direct our development towards a lower environmental and CO2 footprint, but above all towards less energy-intensive processes. The NOF Metal Coatings Group teams, enriched by the younger generation and their talents, will very soon be able to offer new, even more effective and environmentally-friendly solutions for the fastener industry.
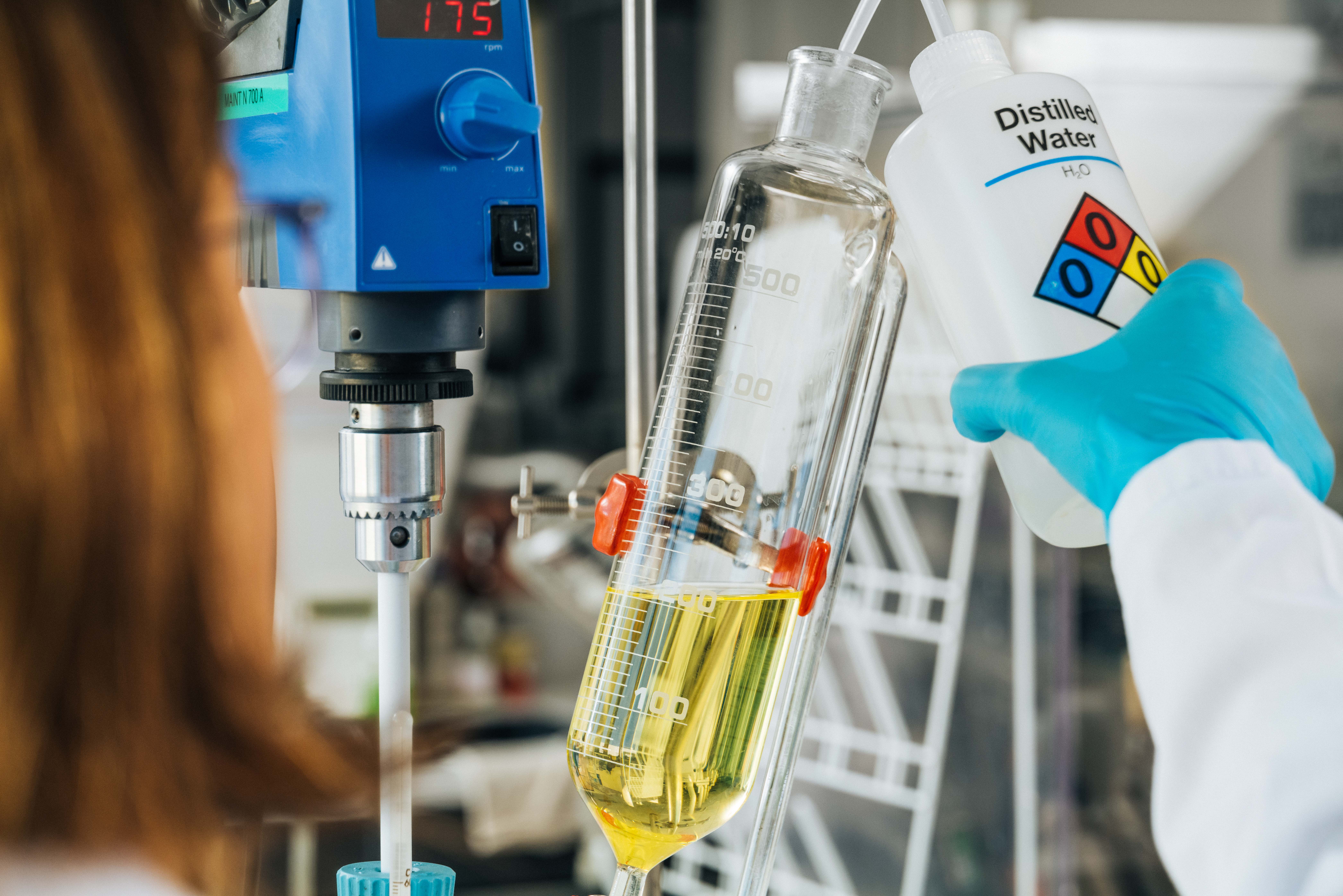
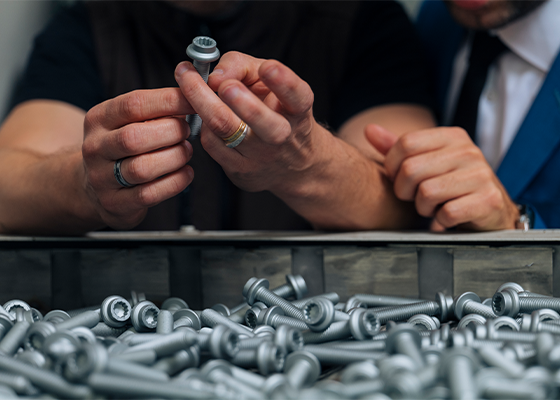